I lunghi viaggi destano sempre una certa ammirazione. Prima di chiudere l’involto che protegge il VAIA Cube e affidarlo al corriere, c’è un istante di meraviglia per il percorso travagliato che quel pezzo di legno ha dovuto compiere. Sappiamo quali difficoltà si celano nella manipolazione di un materiale vivo.
Poco tempo fa, vi abbiamo illustrato la complessità e le sfide della filiera del legno, ma ancora non abbiamo alzato le quinte dietro cui si nasconde la creazione del VAIA Cube. In questo articolo, vi raccontiamo il viaggio del nostro amplificatore passivo seguendolo passo passo in ogni stadio di lavorazione, dal recupero dei tronchi abbattuti fino alle rifiniture finali.
La prima trasformazione
La tempesta di fine ottobre 2018 ha colpito per la maggior parte boschi demaniali. Le procedure di recupero dei fusti sono pertanto piuttosto standardizzate: il primo passo viene portato a termine dai boscaioli, ai quali vengono appaltati i lavori di pulitura ed esbosco da parte dell’ente pubblico. Si tratta di un lavoro complesso e rischioso, specialmente quando si tratta di operare su piante abbattute in maniera casuale e potenzialmente ancora pericolanti – esattamente il caso di VAIA. L’improvviso shock di offerta che ha colpito il mercato del legname a seguito della tempesta, unito al rallentamento dell’economia globale, ha ridotto drasticamente i prezzi di vendita, disincentivando il recupero del legno. Anche per questo motivo, la Provincia Autonoma di Trento ha predisposto degli incentivi per il recupero dei tronchi schiantati, per contrastare la diffusione del bostrico tipografo.
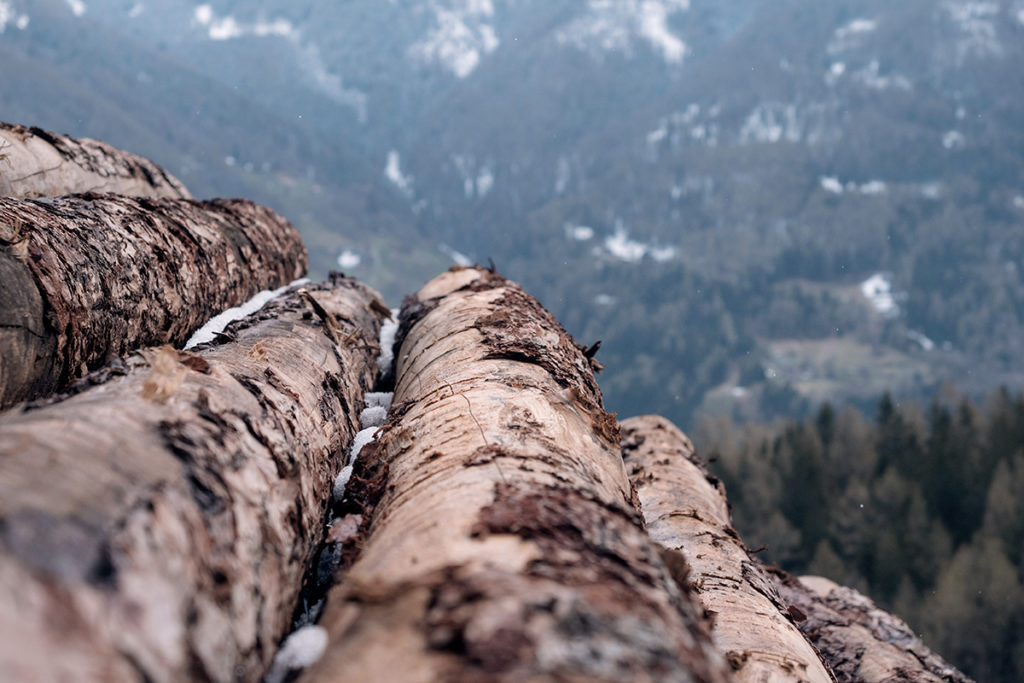
In un secondo momento, il boscaiolo vende i lotti di legname alle segherie, dove avviene la prima fase di lavorazione. Il legno acquistato per i nostri VAIA Cube proviene proprio da queste realtà. Per realizzare l’amplificatore, dobbiamo partire da un formato particolare – il cosiddetto “travetto”, ovvero un pezzo di tronco squadrato e dalla sezione variabile. A seconda del metodo di lavoro della segheria e del materiale a disposizione, abbiamo due possibilità: acquistare i travetti già realizzati, oppure selezionare i tronchi e commissionare la realizzazione dei travetti desiderati alla segheria. L’acquisto avviene in metri cubi di “abete VAIA” e “larice VAIA”, rispettivamente in proporzioni di 3/5 e 2/5 dell’ordinativo complessivo. Le segherie con cui collaboriamo, così come le foreste dalle quali provengono i fusti, sono certificate PEFC, e dichiarano in fase di vendita che il legno è caduto per mano di VAIA.
Come scegliere il legno perfetto
Il legno è un materiale peculiare e imperscrutabile: fino a quando non si comincia a lavorarlo, è impossibile conoscerne la vera qualità. Per dirla con le parole del nostro Giorgio, mastro artigiano, “tagliare un albero è come aprire un uovo di Pasqua”.
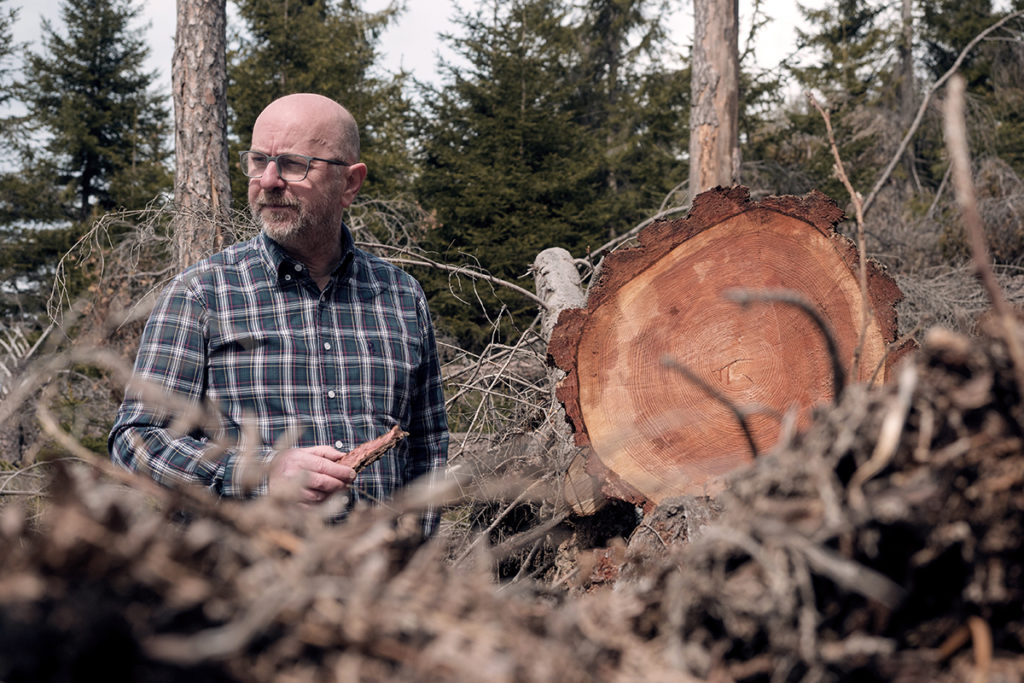
Come avviene dunque questa delicata scelta? Innanzitutto, il fusto deve presentare meno imperfezioni possibili – principalmente nodi, microlesioni o attacchi da parte di insetti. Questa prima ispezione può migliorare il processo di selezione, ma l’artigiano sa che ogni lotto contiene una percentuale di materiale da scartare. Larice e abete sono varietà tipicamente nodose e la rottura dei rami, dovuta ad esempio a grandi nevicate, crea i cosiddetti “nodi cadenti”, che non possono essere in alcun modo lavorati. Il problema dello scarto, intrinseco alla natura di questo materiale così peculiare, è accentuato dal fatto che i grossi quantitativi di legname da smistare hanno ostacolato i normali processi di selezione.
Il legno utilizzato è il cosiddetto “fuori cuore”, ovvero quella parte del tronco esterna al midollo della pianta. In fase di essiccazione, infatti, la fibra lignea del midollo si spacca, e deve quindi essere scartata fin dall’inizio. Poiché la realizzazione del Cube parte da travetti con una sezione di 12×12 centimetri, il tronco deve avere un diametro minimo di 40 centimetri circa.
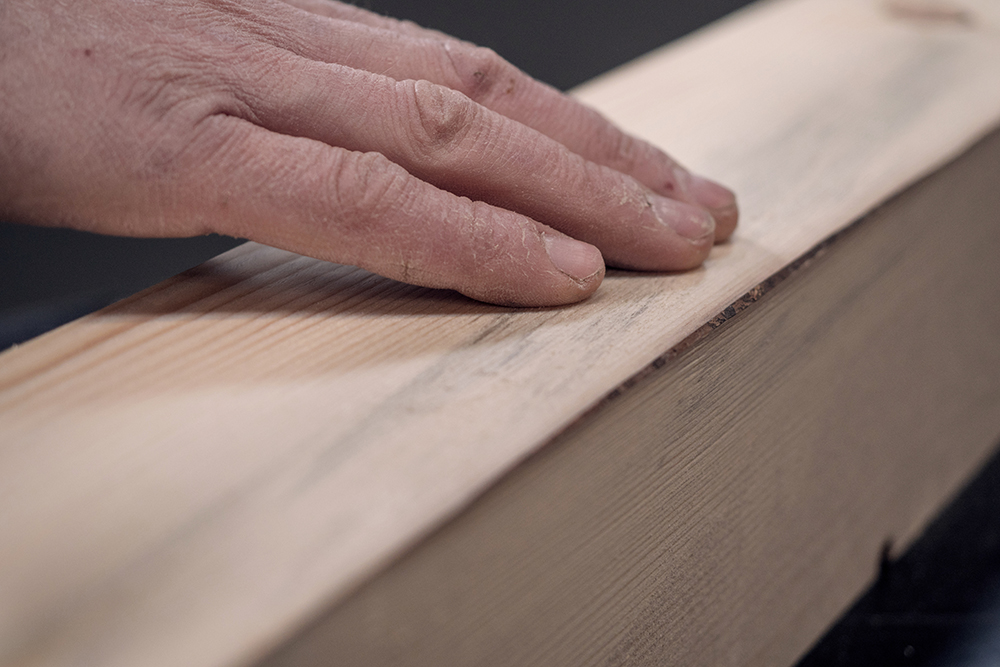
Altro momento molto importante per il percorso del Cubo è appunto la fase di essiccazione: il legno non essiccato si riduce col tempo, ed è difficilmente lavorabile. Per la grande attenzione dedicata a questa fase cruciale, oltre che per la qualità del legname lavorato, ci siamo rivolti alla segheria alto-atesina di Hans Kauffman, che dispone di un moderno forno di essiccazione, assicurando in circa 20 giorni una veloce e ottimale asciugatura.
Ora che abbiamo i nostri bei travetti in larice e abete rosso essiccati, seguiamo il nostro legno nelle fasi della lavorazione finale.
La falegnameria, il laboratorio delle meraviglie
La manifattura dei due legni è molto diversa, e viene per questo affidata a due mastri artigiani. Il larice finisce nella torneria di Angelo Carminati, in Val Brembilla (BG). Lì i morali di larice vengono sezionati in piccoli pezzi, torniti all’esterno e forati all’interno: si ottiene così il cono del VAIA Cube, fondamentale per la propagazione del suono.
L’abete invece viene consegnato alle mani esperte di Giorgio e Marco Leonardelli: è qui che il Cubo prende la sua forma finale. Il primo passaggio consiste nella piallatura dei lati del travetto, asportando il materiale in eccesso per raggiungere una sezione di dimensione 100×92 centimetri. Vengono poi eseguiti i fori per accogliere il cono in larice, e successivamente si procede al taglio per ottenere i veri e propri Cubi.
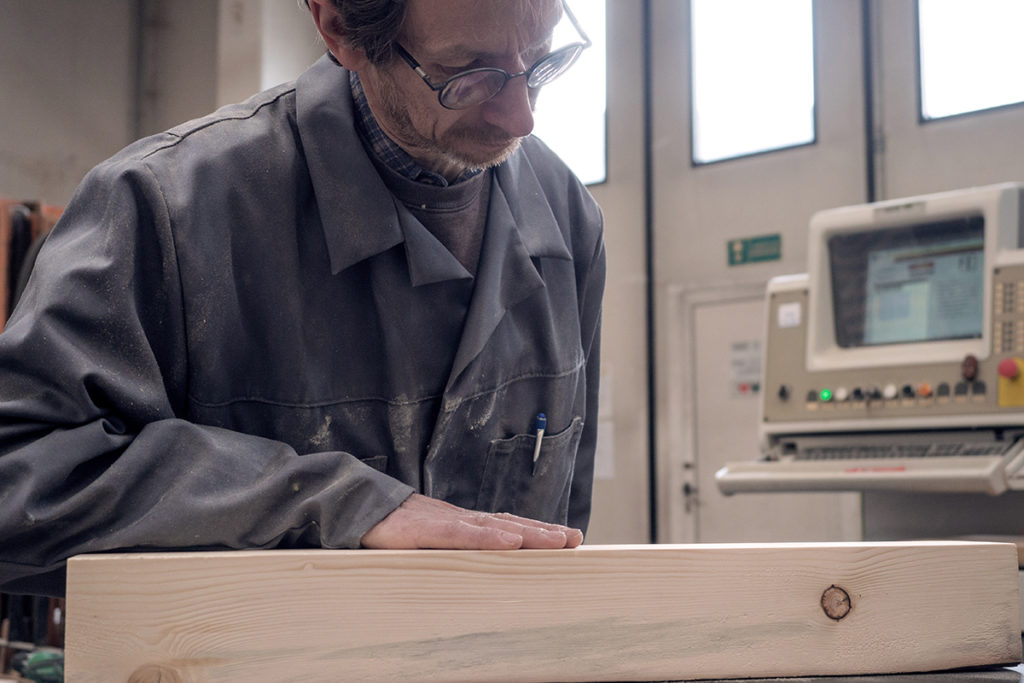
Siamo solo a metà dell’opera! Adesso vanno ricavate le fessure per inserire lo smartphone e per far uscire il cavo di ricarica. La forma è ormai quasi raggiunta: il Cubo è ancora molto spigoloso, e viene attentamente levigato. La marcatura è un’altra fase particolarmente delicata, poiché imprime un segno permanente sulla superficie dell’amplificatore.
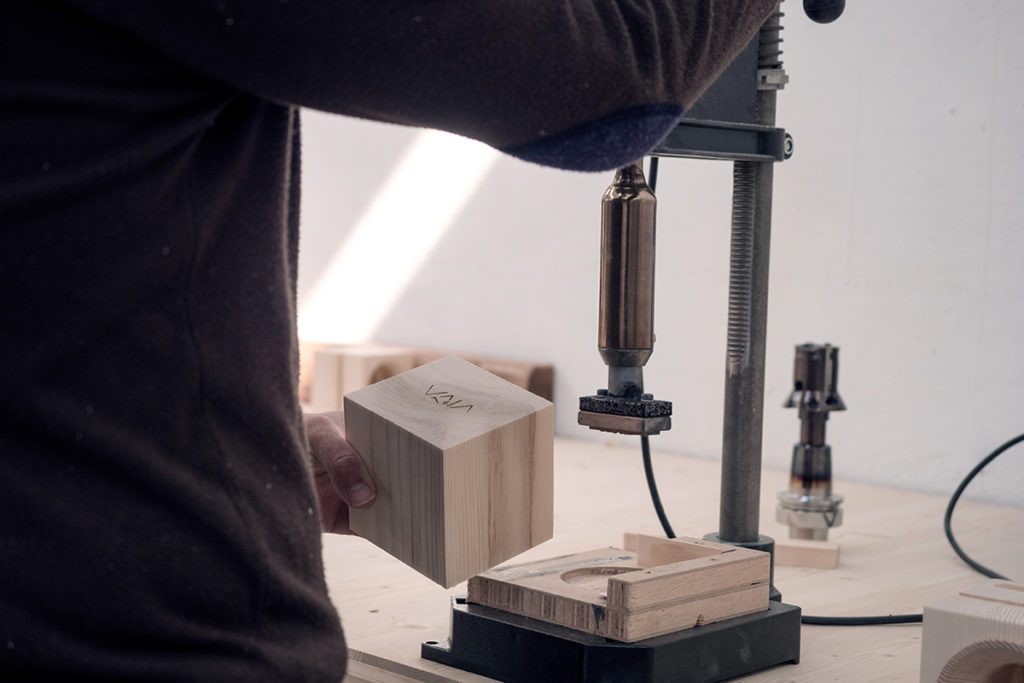
Come potete vedere, il Cubo è ancora integro. È solo ora che interviene il colpo d’ascia a generare la frattura che tutti voi conoscete, per restituire la ferita della foresta.
La falegnameria di Giorgio e Marco è anche il luogo in cui avviene l’assemblaggio: i coni finiti vengono recapitati qui, e poiché ogni pezzo è creato in maniera artigianale si ricerca il cono delle dimensioni giuste per associarlo a ciascun Cubo. Un ultimo lavoro di levigatura dà il tocco finale all’amplificatore passivo più iconico del momento.
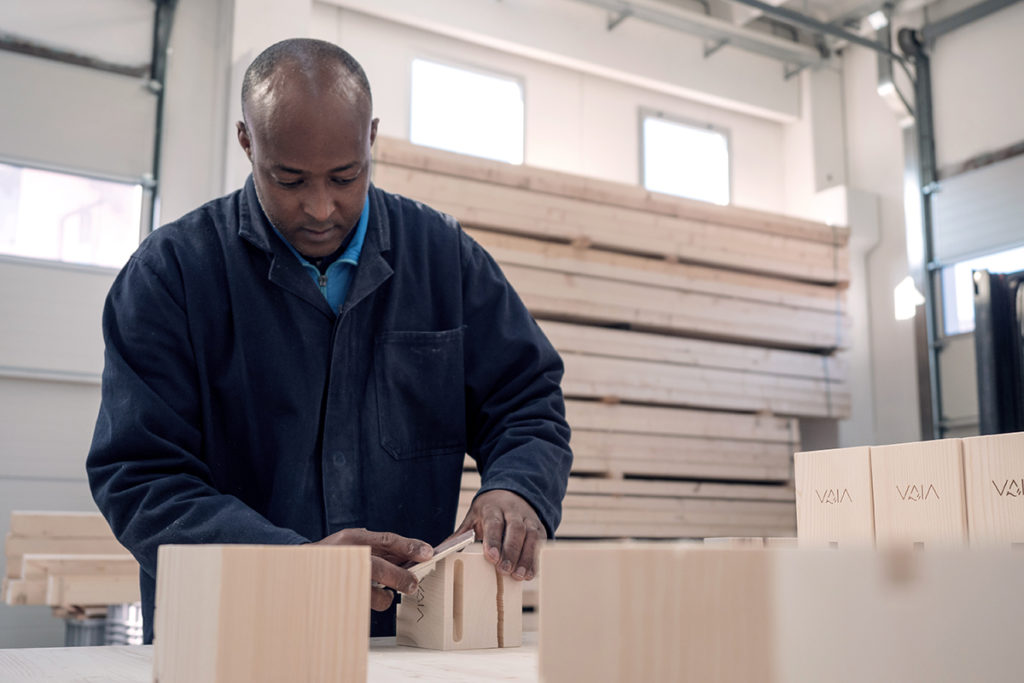
I processi di lavorazione generano inevitabilmente una quantità discreta di scarto. VAIA è particolarmente attenta a una valorizzazione del legno a 360 gradi: i trucioli vengono compressi in falegnameria per ottenere pellet naturali da combustibile.
Riscoprire le origini, abbracciando la novità
Per giungere alla vera genesi di VAIA Cube, bisogna però scavare ancora. Tutto inizia da un modello in noce realizzato a mano dal nonno di Federico, a partire dal quale vengono disegnati i primi prototipi per valorizzare al meglio le tipologie di legname atterrato dalla tempesta. Saltano all’occhio due caratteristiche in particolare: la mancanza della spaccatura, e l’assenza di un cono separato dal corpo dell’oggetto.
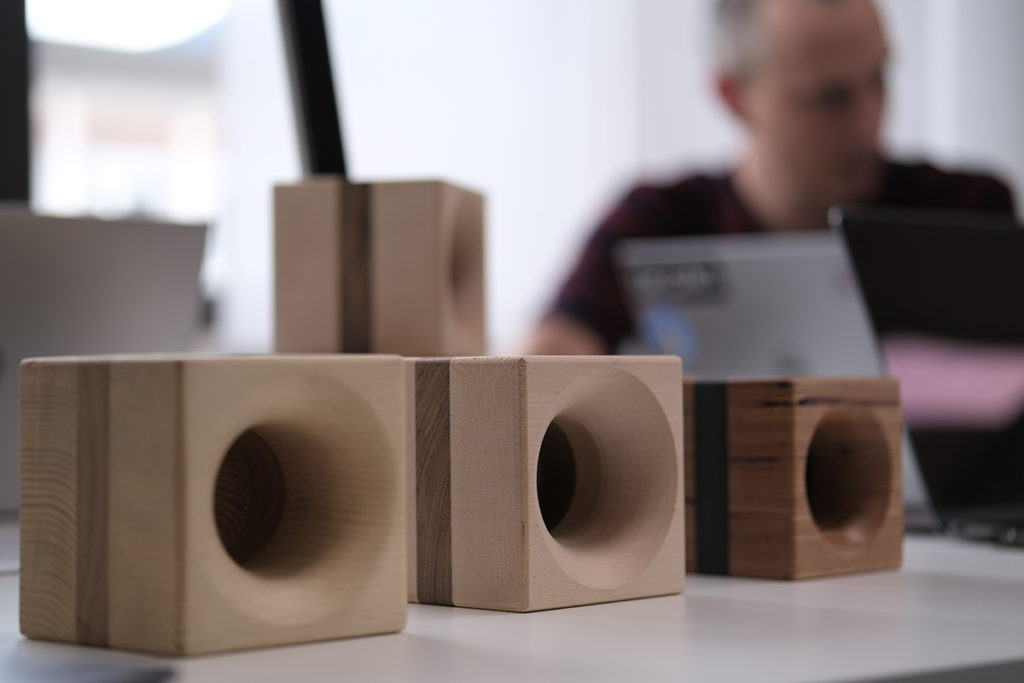
In un prototipo successivo proposto dal nostro designer Gabriele, l’amplificatore rompeva con la forma cubica, e innestava un importante innovazione: la costruzione a incastro. In un lavoro collaborativo di ideazione, l’expertise di Giorgio è intervenuta nell’interpretare il cono come fulcro del gioco di incastri, e nel creare la spaccatura come cerniera di congiunzione tra i due legnami. La forma è rimasta quella originale, per incarnare la perfezione del cubo.
Un’innovazione importante è stata raggiunta con la creazione di VAIA Cube imperfetto, che impiega il legno maggiormente segnato dall’azione degli agenti atmosferici. L’impatto estetico non passa inosservato, e per un oggetto fortemente caratterizzato come il Cube, si è trattato di un passaggio coraggioso e apprezzato dalla community. Ma la nostra ricerca non si ferma qui. I prossimi mesi ci vedranno al lavoro per continuare a valorizzare al meglio questa risorsa preziosa, forti del know how costruito e della collaborazione con gli straordinari professionisti che ci affiancano.