Long journeys inspire a certain admiration. Before we close the wrapping that protects the VAIA Cube and hand it over to the courier, we feel a flash of wonder thinking about the arduous journey that this little piece of wood has made.
A short while ago, we recounted the complexities and challenges of the wood industry, but we still haven’t lifted the lid on the creation of the VAIA Cube. In this article, we tell you about the journey of our passive amplifier, and follow it step by step through each stage of processing, from the recovery of felled logs to the final finishing touches.
The first transformation
The storm at the end of October 2018 affected mostly state-owned forests. Log recovery procedures are therefore fairly standardised: the first step is completed by the loggers, who are contracted by the public authority to carry out the cleaning and logging work. This is a complex and risky job, especially when it involves working on trees that fell uncontrolled and that are thus still potentially unsafe – exactly the case of VAIA. The sudden supply shock that hit the timber market in the wake of the storm, combined with the global economic slowdown, has drastically reduced selling prices, discouraging the salvage of trunks. For this reason too, the Autonomous Province of Trento has set up incentives for the recovery of crashed logs, in order to combat the spread of the bark beetle.
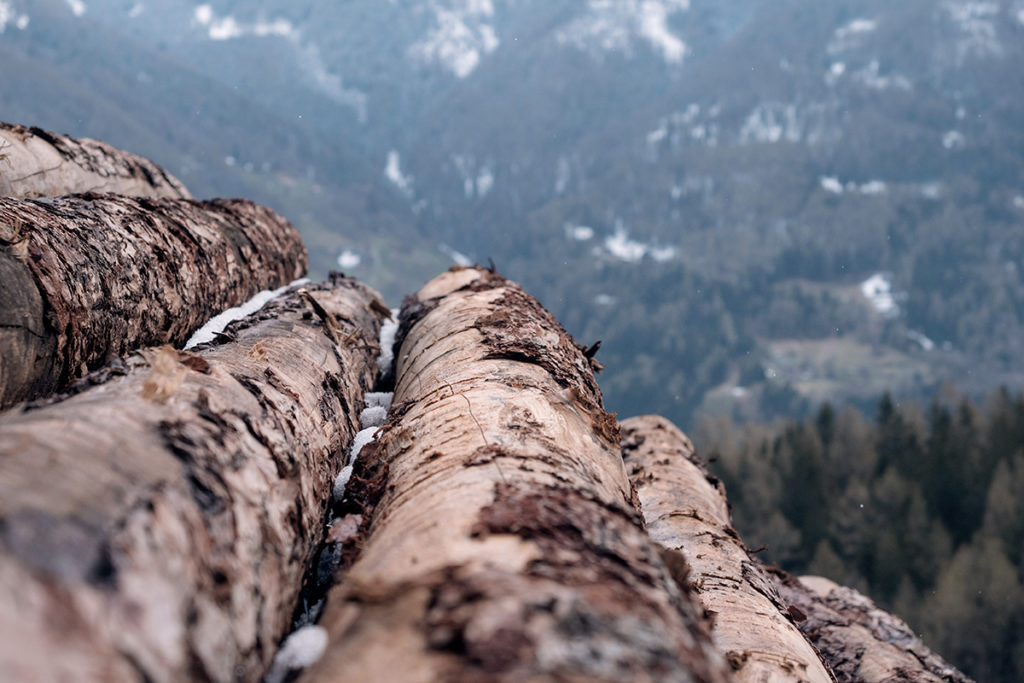
In a second step, the logger sells lumber batches to sawmills, where the first processing phase takes place. The wood we buy for our VAIA Cube comes from there. In order to make the amplifier, we have to start with a particular format – the so-called “joist“, which is a square piece of log with a variable cross-section. Depending on the working method of the sawmill and on the available material, we have two options: either we buy already made joists, or we select the logs and commission the sawmill to make them. The purchase is made in cubic metres of “VAIA spruce” and “VAIA larch”, in proportions of 3/5 and 2/5 of the total order respectively. The sawmills we work with, as well as the forests from which the logs come, are PEFC certified, and declare at the time of sale that the wood has fallen by the hand of VAIA.
How to choose the perfect wood
Wood is a peculiar and inscrutable material: until you start working with it, it is impossible to know its true quality. In the words of our master craftsman Giorgio, “cutting down a tree is like opening an Easter egg”.
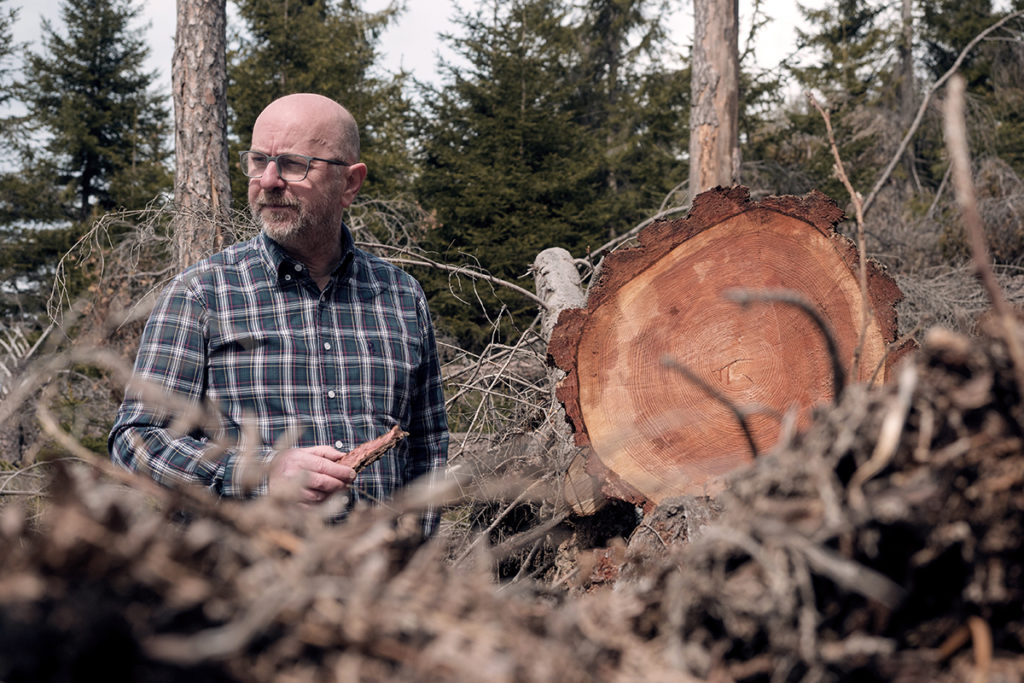
So how is this delicate choice made? First of all, the trunks must have as few imperfections as possible – mainly knots, micro-lesions or insect attacks. This initial inspection can improve the selection process, but the craftsman knows that each batch contains a percentage of material that will be discarded. Larch and spruce are typically gnarled varieties and branch breakages, e.g. due to large snowfalls, create gnarls that cannot be processed in any way. The problem of waste, intrinsic to the nature of this peculiar material, is accentuated by the fact that the large quantities of trunks to be sorted have hampered the usual selection processes.
The wood that can be used, out of a trunk cross-section, is the part outside of the pith. Pith’s wood fibre splits and cracks when the timber is dried, and has to be discarded from the start. Since the Cube is made from joists with a section of 12×12 centimetres, the trunk must have a minimum diameter of about 40 centimetres.
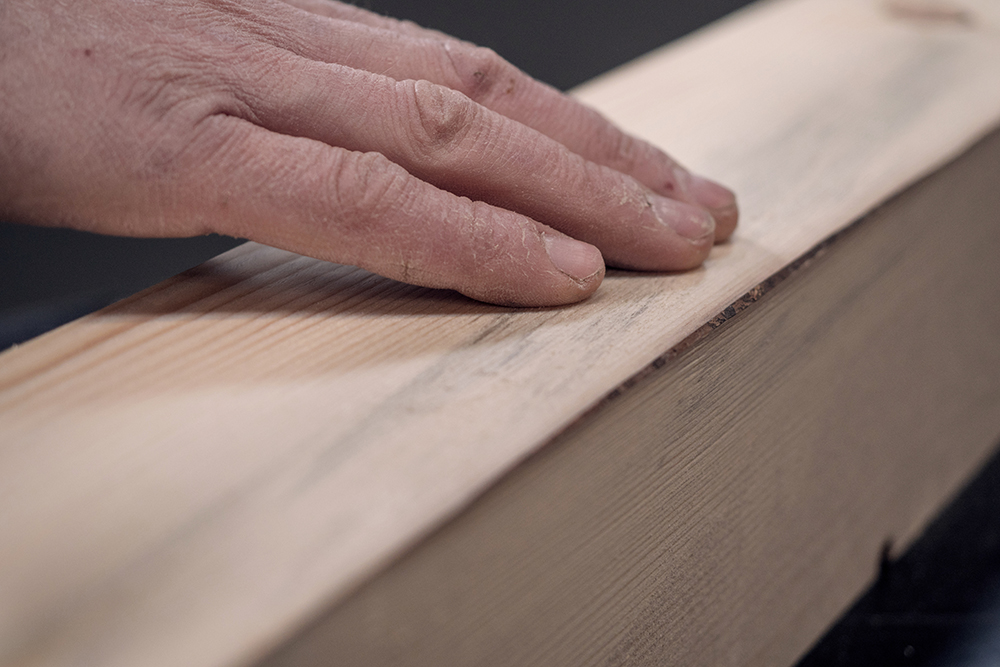
Another very important moment in the Cube’s journey is the drying phase: undried wood shrinks over time, and is difficult to work. Because of the great attention paid to this crucial step, as well as the quality of the processed timber, we have turned to Hans Kauffman’s South Tyrolean sawmill, which has a modern drying oven that ensures fast and optimum drying in about 20 days.
Now that we have our beautiful, dried larch and spruce joists, we follow our wood through the final processing stages.
The carpenter’s shop, source of wonder
The manufacture of the two woods is very different, and is therefore entrusted to two master craftsmen. The larch ends up in Angelo Carminati’s turnery in Val Brembilla (BG). There, the larch joists are cut into small pieces, lathed on the outside and drilled on the inside: this is how the VAIA Cube’s cone is obtained, which is fundamental for sound propagation
The spruce, on the other hand, is handed over to the expert hands of Giorgio and Marco Leonardelli: this is where the Cube takes its final shape. The first step is to lathe the sides of the joist, so as to remove excess material and achieve a cross-section of 100×92 centimetres. Openings are drilled to accommodate the larch cone, and then the actual cubes are cut.
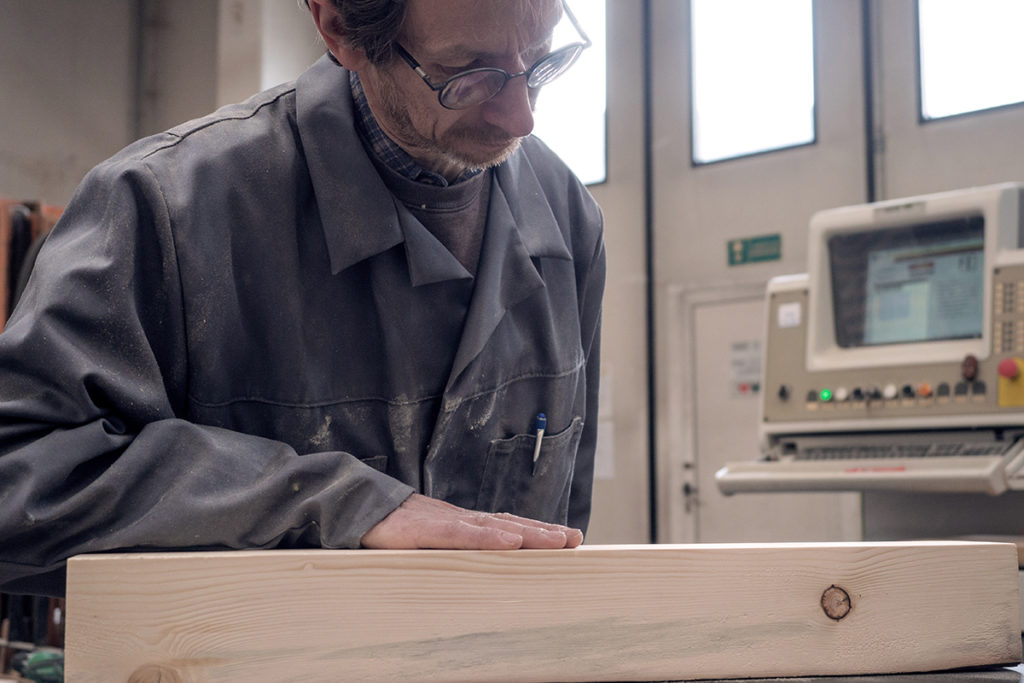
We are only halfway through the work! Now we have to prepare the slots for the smartphone and for the charging cable. The final shape is almost achieved: the Cube is still sharp-cornered, and is carefully polished. The marking is another particularly delicate step, since it leaves a permanent trace on the amplifier’s surface.
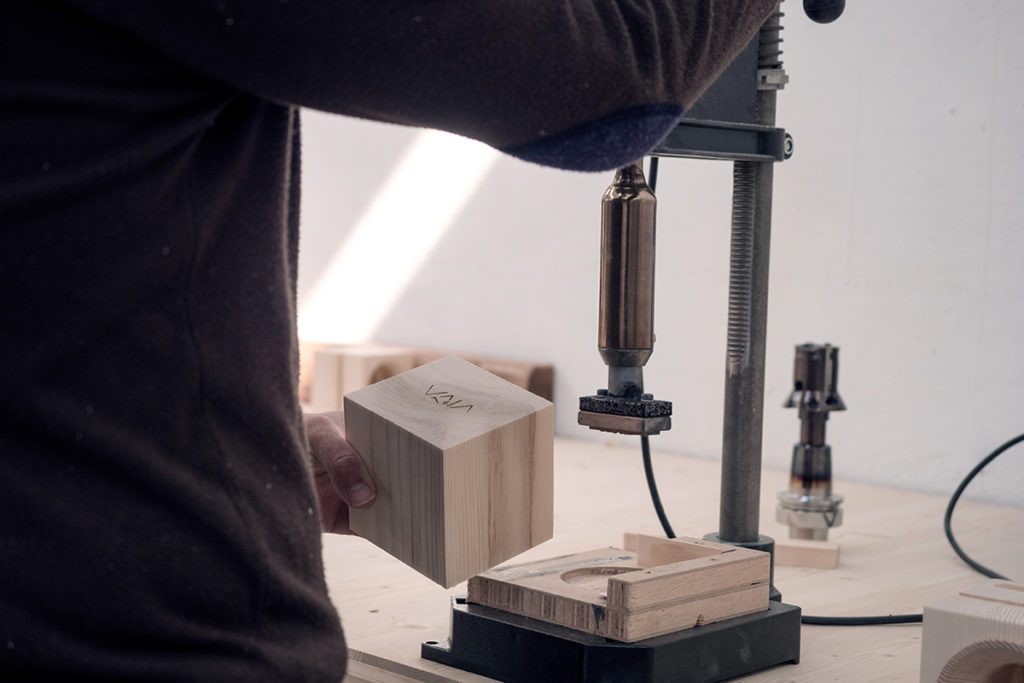
As you can see, the Cube is still intact. It is only now that the axe blow generates the fracture you all know, to imprint the wound of the forest.
Giorgio and Marco’s carpenter’s shop is also where the assembly takes place: the finished cones are delivered here, and since each piece is created by hand, the right one has to be sought after in order to associate it with each Cube. A last polishing job puts the finishing touches to the most iconic passive amplifier of the moment.
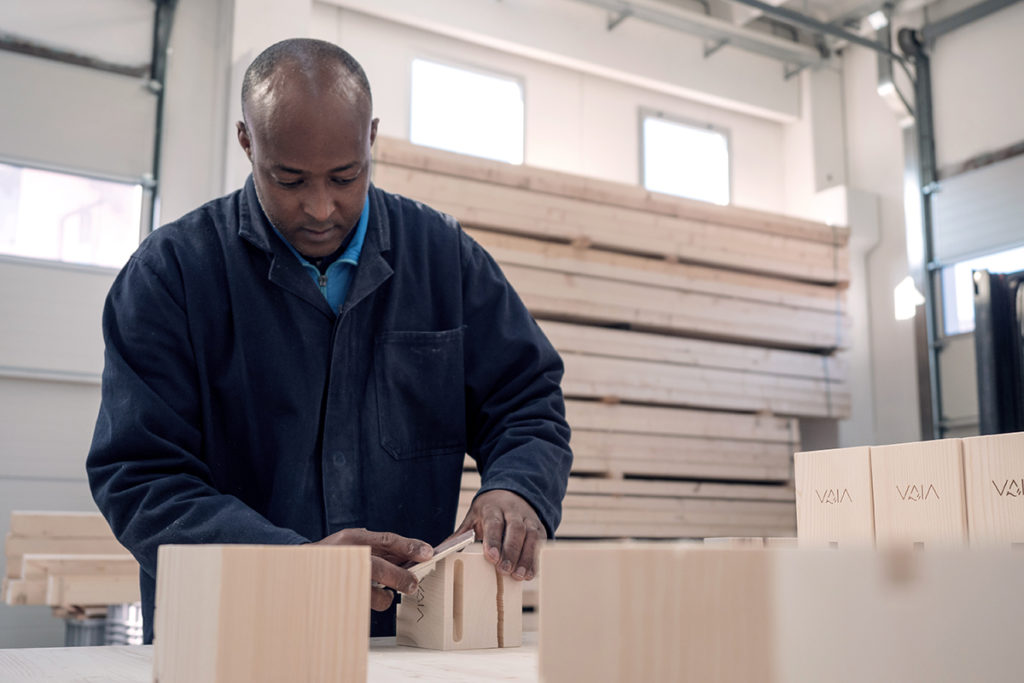
Manufacturing processes inevitably generate a fair amount of waste. VAIA pays particular attention to the all-round use of wood: the chips are compressed on site to obtain natural fuel pellets.
The very first steps: a throwback
To get to the real genesis of the VAIA Cube, we have to dig a little further. It all starts with a walnut wood model made by Federico’s grandfather, which provided the inspiration for the first prototypes. Two features in particular stand out: the lack of a split, and the absence of a cone separated from the body of the object.
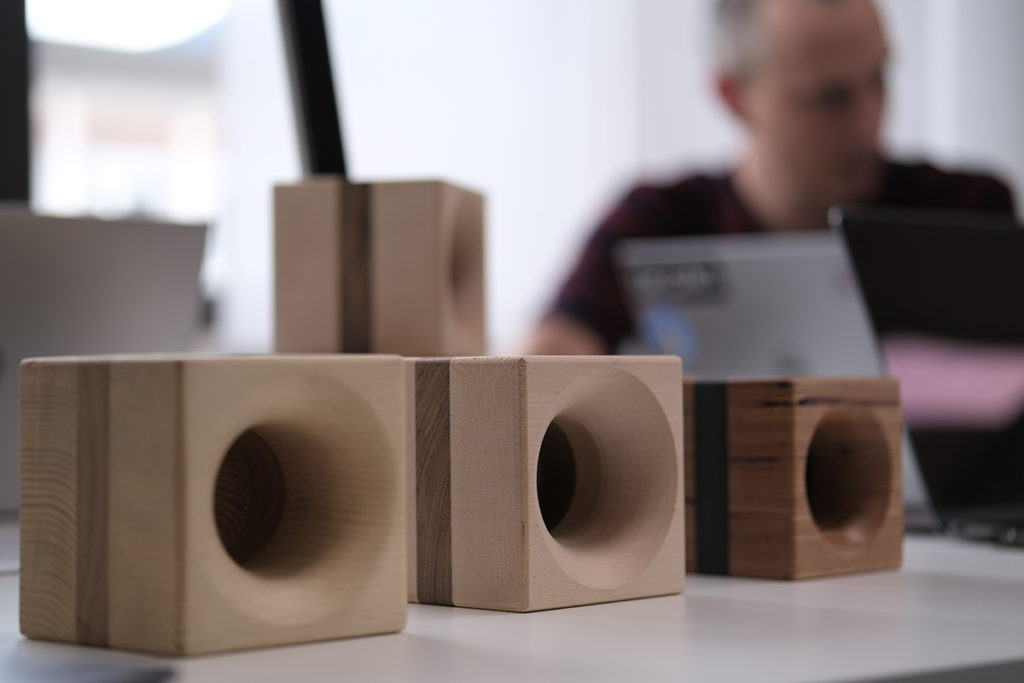
In a later prototype proposed by our designer Gabriele, the amplifier broke with the cubic shape and introduced an important innovation: interlocking structures. In a collaborative design process, Giorgio’s expertise intervened in interpreting the cone as the fulcrum of the jigsaw, and in creating the split as a gateway to join the two pieces of wood. The shape remained the original one, to embody the perfection of the cube.
An important innovation was achieved with the creation of VAIA Cube imperfetto, which uses the wood most affected by atmospheric agents. The aesthetic impact does not go unnoticed, and for an object as strongly characterised as the Cube, it was a courageous step that was appreciated by the community. But our search doesn’t stop here. The next months will see us working to continue to make the most of this precious resource, thanks to the know-how we have built and to the collaboration of extraordinary professionals who work alongside us.